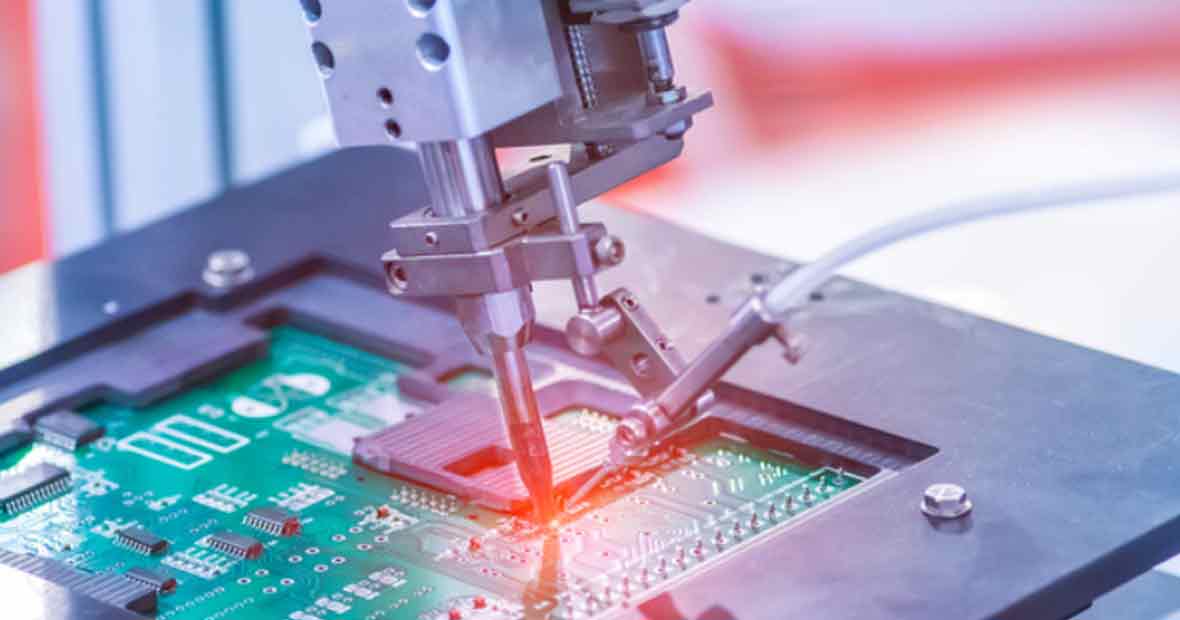
Delving into the complex world of Printed Circuit Board (PCB) production, one finds that quality assurance stands as a pillar of paramount importance. This process plays an instrumental role in elevating PCB performance, minimizing defects, and ensuring the longevity of the final products. This piece sheds light on the key quality assurance measures employed within PCB manufacturing. From strict control in assembly and fabrication to the utilization of materials of the highest standards, these measures are wide-ranging. Further, the importance of meticulous component checking and testing is highlighted, emphasizing the pivotal role of inspection in PCB quality control. Lastly, the article discusses the certification requisites and the impact of automated technology on PCB quality assurance.
Importance of Quality Assurance in PCB Production
Quality Assurance, a crucial part of any manufacturing process, plays an especially significant role in the production of PCBs. It acts as a guiding force, ensuring the consistent production of high-quality and reliable PCBs.
Role of Quality Assurance in Enhancing PCB Performance
A detailed guide explains that Quality Assurance measures are pivotal to enhance the performance of PCBs. These measures are instrumental in maintaining the integrity of electronic components within each circuit board and ensuring the smooth functioning of the end product.
Quality Assurance Measures to Minimize Defects
A webinar presents various strategies of Quality Assurance, focusing on how these measures can effectively minimize defects in PCB production. Case studies and examples are provided, showcasing effective solutions and tips to resolve common quality issues in PCB manufacturing.
Quality Assurance for Longevity of PCB Products
An e-book suggests that Quality Assurance can significantly increase the longevity of PCB products. It offers practical techniques and advice to maintain consistent quality. A regular newsletter from icape-group.com provides updates on the latest technologies and practices in Quality Assurance for PCB production.
Key Quality Assurance Measures in PCB Manufacturing
Quality assurance plays a crucial role in the success of Printed Circuit Board (PCB) production. It necessitates the undertaking of several vital measures aimed at ensuring that the PCBs manufactured meet the highest standards possible.
Quality Control in Assembly and Fabrication
The assembly and fabrication process of PCBs involves meticulous checks and controls. These measures ensure that each circuit board manufactured adheres to the pre-set standards. The quality control process includes critical steps like soldering and component placement, where precision is of utmost importance.
Role of High Standards Materials in PCB Manufacturing
Quality assurance in PCB manufacturing is not limited to checks and controls during the assembly process. The use of high standard materials also plays a critical role in the overall quality of the product. Materials chosen must be of a high standard to ensure they can withstand the manufacturing process and perform optimally in the final product.
Checking and Testing Components for Quality Assurance
Another key aspect of quality assurance in PCB manufacturing is the checking and testing of components. Every component used in the assembly of PCBs needs to be thoroughly tested to ensure it functions as expected. This step is crucial for maintaining the quality and reliability of the final product.
Below are some strategies and tips for integrating quality assurance measures smoothly into the PCB production process:
Selection of appropriate quality assurance measures based on the specific requirements of the PCB production.
Use of evaluation tools and methods for improving the efficiency of the quality assurance measures.
Cost analysis and case studies demonstrating the long-term return on investment of quality assurance measures in PCB manufacturing.
Role of Inspection and Testing in PCB Quality Control
Quality assurance in PCB production heavily relies on meticulous inspection and testing processes. Each PCB undergoes rigorous tests and inspections to guarantee the highest level of quality and performance. The process serves to identify potential defects and issues with the circuit boards, thus assuring electrical and electronic components' reliability on the final product.
The importance of inspection and testing in PCB quality control is paramount. Through detailed scrutiny and practical application of various testing methods, it is possible to enhance the performance of PCBs significantly. Each testing method offers unique advantages and disadvantages, thereby offering a comprehensive approach to quality control. For instance, some tests focus on the integrity of the board, others on the functionality of the components, and some on the final contact points.
Detailed checklists serve to identify common defects and issues that testing can detect. By addressing these potential issues, it becomes possible to resolve them before the final production phase. Implementing an effective inspection and testing program ensures that all PCBs meet the highest standards of quality, thus reducing the chances of performance issues in the final product.
Real-world cases and examples illustrate how inspection and testing procedures can improve PCBs' final performance. These studies serve as a testament to the effectiveness and importance of rigorous quality control measures in PCB production.
Standards and Certification Requisites for PCB Production
Every manufacturer involved in the production of Printed Circuit Boards (PCBs) should be familiar with various international standards such as the IPC-A-610, IPC-6012, among others. These standards, along with respective certification processes, ensure the quality and safety of PCB products. The relevance of these standards varies across different industries, but adherence is universally beneficial.
Standards and certifications have a significant impact on the production cost of PCBs. However, non-compliance can lead to adverse consequences that may far outweigh the initial cost. Selecting a PCB supplier who adheres to the appropriate standards and certifications is therefore a critical decision.
These standards and certifications guarantee the durability and reliability of PCBs. Recent updates or modifications to these standards require careful attention. Each country or region may have specific standards and certifications, presenting challenges for manufacturers seeking certification for PCB production.
The environmental impact of PCB production has led to the emergence of ecological standards. Compliance with these standards is critical for the import and export of PCBs. Understanding and respecting these standards and certifications requires training.
Looking ahead, future trends in standards and certifications for PCB production will likely continue to evolve. Quality testing and inspections are essential to meet these standards and certifications. Various educational resources are available for deeper understanding of PCB production standards and certifications.
Impact of Automated Technology on PCB Quality Assurance
Automated technology significantly influences the quality assurance measures in PCB production. Harnessing the potential of automation leads to an enhancement of PCB quality and reliability. This advanced technology, which includes Automated Optical Inspection (AOI) and X-ray inspection, is extensively used by PCB board manufacturers. These technologies meticulously examine PCBs and their components, eliminating potential errors and improving overall performance.
Automated inspection plays a pivotal role in maintaining the quality of PCBs. It allows for the detection and rectification of flaws early in the process, thereby preventing costly reworks. Automated systems are capable of inspecting circuit boards at a speed and accuracy that far surpasses manual methods. This results in substantial cost savings in quality assurance services.
These resources highlight the vital role of automated technology in enhancing the design and production of electronic components, particularly PCBs. Thereby, underscoring the significance of investing in automated systems for PCB quality assurance.