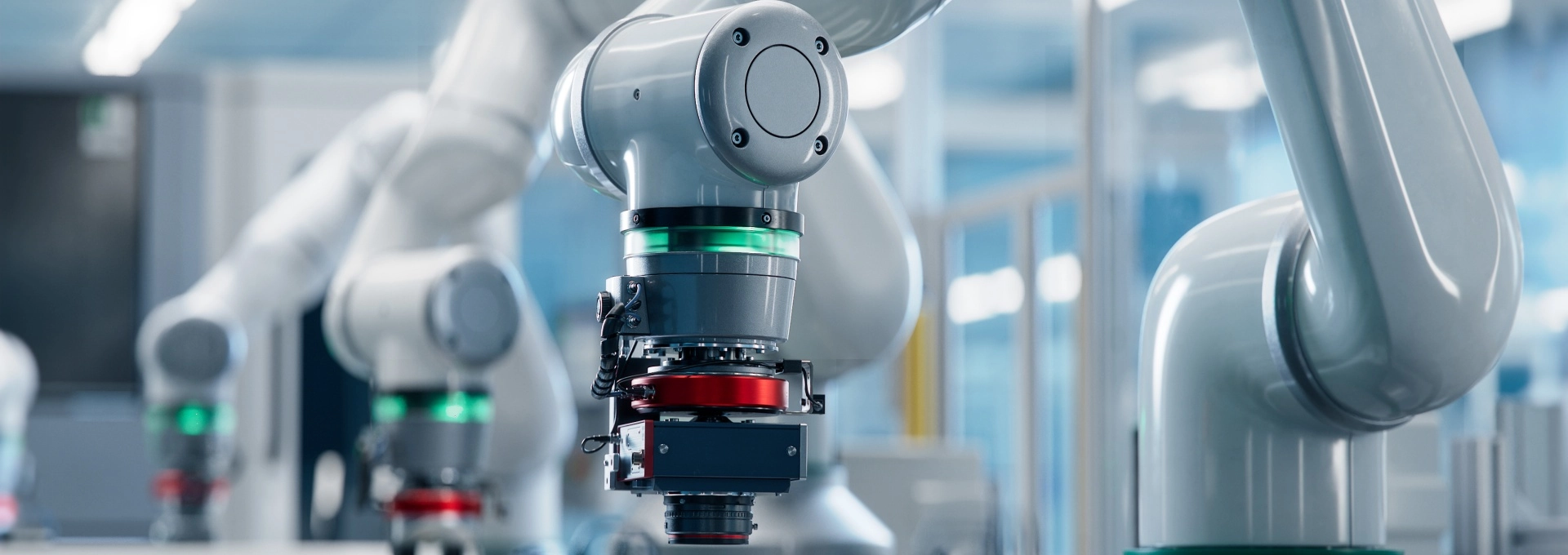
The semiconductor industry stands at the forefront of technological innovation, driving advancements in computing power, energy efficiency, and miniaturization. As demand for smaller, faster, and more powerful electronic devices continues to grow, the machines responsible for producing these intricate components must evolve to meet increasingly stringent requirements. From photolithography systems to advanced etching technologies, the realm of semiconductor production is undergoing a transformative revolution, pushing the boundaries of what's possible in chip manufacturing.
Evolution of photolithography systems in semiconductor fabrication
Photolithography remains the cornerstone of semiconductor fabrication, serving as the primary method for creating intricate circuit patterns on silicon wafers. Over the years, this technology has undergone significant advancements to keep pace with Moore's Law and the industry's relentless drive towards smaller transistor sizes.
The transition from traditional deep ultraviolet (DUV) lithography to extreme ultraviolet (EUV) lithography marks a pivotal moment in semiconductor manufacturing. EUV systems, operating at a wavelength of 13.5 nanometers, enable the production of chips with features as small as 7 nanometers and beyond. This leap in precision has opened up new possibilities for chip designers, allowing for the creation of more complex and efficient integrated circuits.
One of the key challenges in EUV lithography has been the development of reliable light sources. Innovative approaches, such as laser-produced plasma (LPP) technology, have emerged to generate the intense EUV light required for this process. These advancements have been crucial in making EUV lithography commercially viable for high-volume manufacturing.
As the industry pushes towards even smaller node sizes, researchers are exploring next-generation lithography techniques. High-numerical-aperture (high-NA) EUV systems promise to extend the capabilities of EUV lithography, potentially enabling feature sizes below 3 nanometers. This continuous evolution in photolithography systems underscores the industry's commitment to overcoming technological barriers and driving semiconductor innovation forward.
Advanced etching technologies: plasma and reactive ion etching
Etching processes play a critical role in semiconductor fabrication, shaping the intricate structures that form the foundation of modern integrated circuits. As device geometries shrink and complexity increases, advanced etching technologies have become indispensable for achieving the precision and control required in cutting-edge chip production.
Plasma etching and reactive ion etching (RIE) have emerged as dominant techniques in the semiconductor industry, offering superior control over etch profiles and selectivity. These methods utilize energized gases to create a plasma that selectively removes material from the wafer surface, allowing for the creation of complex three-dimensional structures at the nanoscale.
The semi-conductor production machine repair company plays a crucial role in maintaining and optimizing these advanced etching systems, ensuring their continuous operation and peak performance in high-volume manufacturing environments. As etching technologies continue to evolve, the expertise of specialized repair and maintenance services becomes increasingly valuable to semiconductor manufacturers.
High-aspect-ratio etching with bosch process
The Bosch process has revolutionized the creation of deep, high-aspect-ratio features in silicon, enabling the production of advanced MEMS devices and through-silicon vias (TSVs) for 3D chip stacking. This cyclic etching technique alternates between etching and passivation steps, allowing for the formation of nearly vertical sidewalls with exceptional depth control.
Atomic layer etching for nanoscale precision
As device dimensions approach atomic scales, atomic layer etching (ALE) has emerged as a powerful technique for achieving unprecedented precision in material removal. ALE offers angstrom-level control over etch depth, making it invaluable for fabricating next-generation transistor structures and advanced memory devices.
Cryogenic etching for temperature-sensitive materials
Cryogenic etching techniques have opened up new possibilities for processing temperature-sensitive materials and achieving ultra-high selectivity. By cooling the wafer to extremely low temperatures during the etching process, unwanted chemical reactions can be suppressed, enabling more precise control over etch profiles and reducing damage to underlying layers.
Laser-assisted plasma etching in 3D NAND production
The production of 3D NAND flash memory has driven the development of innovative etching techniques, including laser-assisted plasma etching. This hybrid approach combines the precision of laser ablation with the versatility of plasma etching, enabling the creation of high-aspect-ratio holes and trenches critical for vertically stacked memory cells.
Deposition techniques: chemical vapor deposition and atomic layer deposition
As semiconductor devices continue to shrink and incorporate more complex materials, advanced deposition techniques have become essential for creating ultra-thin films and precise material stacks. Chemical vapor deposition (CVD) and atomic layer deposition (ALD) stand out as key technologies in this domain, offering unparalleled control over film thickness, composition, and uniformity.
MOCVD for III-V compound semiconductors
Metal-organic chemical vapor deposition (MOCVD) has become the method of choice for growing high-quality III-V compound semiconductor layers. This technique enables the precise control of material composition and doping profiles, critical for the production of advanced optoelectronic devices and high-frequency transistors.
PECVD for low-temperature dielectric layers
Plasma-enhanced chemical vapor deposition (PECVD) has revolutionized the deposition of dielectric layers at lower temperatures, making it possible to integrate sensitive materials and reduce thermal budgets in advanced process nodes. This technique is particularly valuable for depositing passivation layers and inter-metal dielectrics in complex chip designs.
ALD for high-k gate dielectrics in finfet structures
Atomic layer deposition has proven indispensable in the fabrication of high-k gate dielectrics for advanced transistor structures such as FinFETs. ALD's ability to deposit ultra-thin, highly conformal films with precise thickness control has enabled the scaling of gate oxides to just a few atomic layers, crucial for maintaining electrostatic control in nanoscale devices.
Selective area ALD in advanced node manufacturing
Selective area ALD is emerging as a powerful technique for depositing materials only where they are needed, reducing the need for subsequent etching steps and enabling self-aligned processes. This approach is particularly promising for the fabrication of next-generation logic and memory devices, offering a path to further miniaturization and improved device performance.
Wafer inspection and metrology advancements
As semiconductor manufacturing processes become increasingly complex, the role of wafer inspection and metrology in ensuring product quality and yield has never been more critical. Advanced inspection and measurement technologies are essential for detecting defects, verifying process uniformity, and maintaining tight control over critical dimensions.
Optical inspection systems have evolved to incorporate deep ultraviolet (DUV) and even vacuum ultraviolet (VUV) light sources, enabling the detection of ever-smaller defects on wafer surfaces. These systems employ sophisticated algorithms and machine learning techniques to classify defects and identify potential yield-limiting issues early in the manufacturing process.
Electron beam inspection (EBI) technologies have pushed the boundaries of defect detection to the nanoscale, offering the resolution necessary to identify critical defects in advanced logic and memory devices. Multi-beam systems have dramatically increased throughput, making e-beam inspection viable for in-line monitoring in high-volume manufacturing environments.
In the realm of metrology, advanced techniques such as optical critical dimension (OCD) measurement and X-ray metrology have become indispensable for characterizing complex 3D structures and multi-layer stacks. These non-destructive measurement methods provide crucial feedback for process control and optimization, ensuring that devices meet stringent performance and reliability requirements.
Next-generation doping methods: ion implantation and in-situ doping
Precise control over dopant concentration and distribution is fundamental to semiconductor device performance. As device dimensions continue to shrink, traditional doping methods face increasing challenges in achieving the required precision and uniformity. This has led to the development of innovative doping techniques tailored to the demands of advanced node manufacturing.
Plasma doping for ultra-shallow junctions
Plasma doping (PLAD) has emerged as a powerful alternative to traditional beam-line ion implantation for creating ultra-shallow junctions in advanced logic devices. By immersing the wafer in a plasma containing the dopant species, PLAD can achieve more conformal doping profiles and reduce channeling effects, critical for the formation of source/drain regions in nanoscale transistors.
Cluster ion beam technology for reduced channeling
Cluster ion beam implantation offers unique advantages for doping crystalline materials, particularly in reducing channeling effects and minimizing damage to the crystal lattice. By using molecular or cluster ions instead of atomic species, this technique can achieve shallower and more abrupt doping profiles, essential for the fabrication of high-performance devices.
Monolayer doping for 2D materials
The rise of two-dimensional materials like graphene and transition metal dichalcogenides has necessitated the development of novel doping approaches. Monolayer doping techniques, which involve the controlled adsorption and diffusion of dopants on material surfaces, offer a promising route for precisely tailoring the electronic properties of these atomically thin materials.
Gas-phase doping in epitaxial growth processes
In-situ doping during epitaxial growth processes has gained prominence for creating precisely controlled doping profiles in compound semiconductor devices. Techniques such as delta doping and digital alloy growth enable the creation of complex heterostructures with atomically abrupt interfaces, critical for high-frequency and optoelectronic applications.
Integration of AI and machine learning in semiconductor equipment
The semiconductor industry is at the forefront of adopting artificial intelligence (AI) and machine learning (ML) technologies to enhance manufacturing processes and equipment performance. These advanced computational techniques are being integrated across the entire semiconductor production chain, from design and simulation to process control and yield optimization.
In lithography, AI algorithms are being employed to optimize mask designs and improve pattern fidelity, particularly for complex multi-patterning schemes used in advanced nodes. Machine learning models can predict and correct for process variations, enabling tighter control over critical dimensions and reducing edge placement errors.
Etching and deposition processes are benefiting from AI-driven recipe optimization and endpoint detection. By analyzing vast amounts of sensor data in real-time, ML algorithms can make fine adjustments to process parameters, ensuring consistent results across wafers and lots. This adaptive control is particularly valuable for managing the increasing complexity of multi-layer stacks and high-aspect-ratio structures.
Predictive maintenance powered by AI is revolutionizing equipment uptime and reliability. By analyzing sensor data and historical performance metrics, these systems can forecast potential failures and schedule maintenance activities proactively, minimizing unplanned downtime and improving overall equipment effectiveness (OEE).
As the semiconductor industry continues to push the limits of physics and engineering, innovations in production machines will play a pivotal role in shaping the future of electronics. From the nanoscale precision of EUV lithography to the atomic-level control offered by ALD and ALE, these advanced technologies are enabling the creation of more powerful, efficient, and sophisticated semiconductor devices.
The ongoing evolution of semiconductor production machines underscores the industry's commitment to overcoming technological barriers and driving innovation forward. As we look to the future, the convergence of advanced manufacturing techniques with AI and ML promises to unlock new levels of efficiency, precision, and productivity in semiconductor fabrication, paving the way for the next generation of electronic devices that will shape our world.