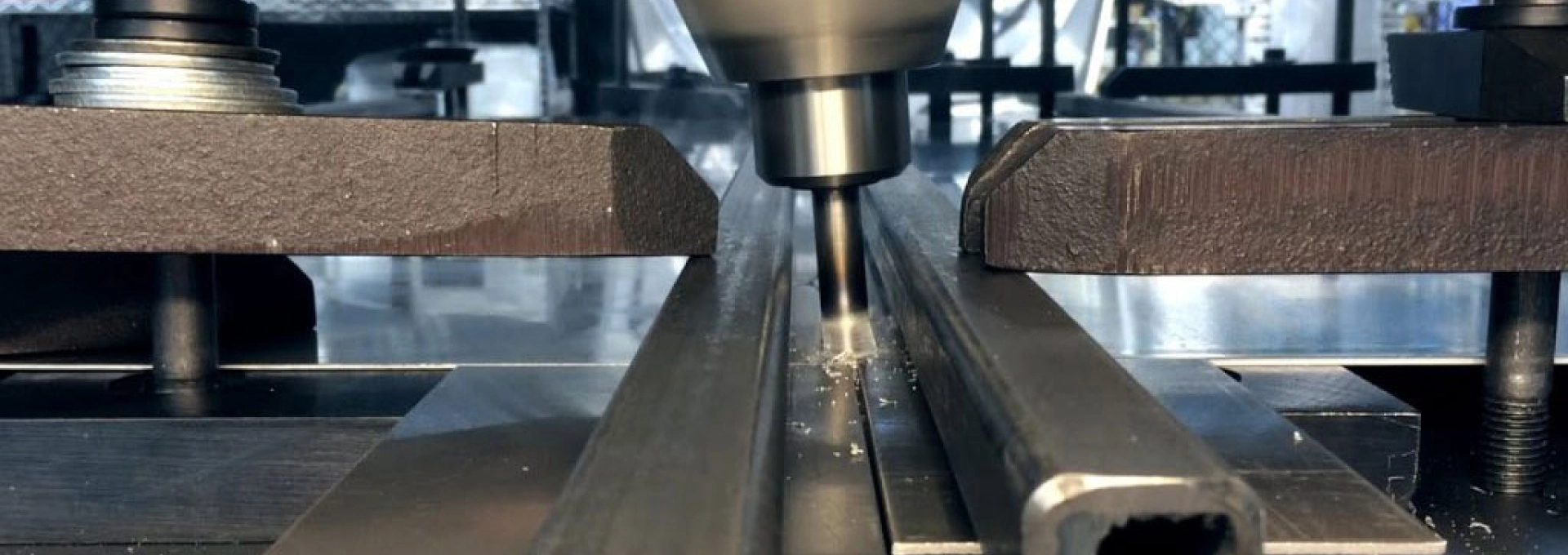
Friction stir welding (FSW) has revolutionized the joining of metals, particularly aluminum alloys, in various industries. This solid-state welding technique offers numerous advantages over traditional fusion welding methods, including reduced distortion, improved mechanical properties, and the ability to join dissimilar materials. However, achieving optimal weld quality requires a thorough understanding of the process parameters and their intricate relationships.
As the demand for lightweight structures in aerospace, automotive, and marine applications continues to grow, mastering the art and science of FSW becomes increasingly crucial. By delving into the fundamental principles, critical process parameters, and advanced optimization techniques, engineers and researchers can unlock the full potential of this innovative welding technology.
Fundamental principles of friction stir welding (FSW)
The friction stir welding process relies on the generation of frictional heat and plastic deformation to create a solid-state joint. A non-consumable rotating tool, consisting of a shoulder and a pin, is plunged into the abutting edges of the workpieces to be joined. As the tool rotates and traverses along the joint line, it generates heat through friction and severe plastic deformation, softening the material without reaching its melting point.
This unique welding mechanism offers several advantages over conventional fusion welding techniques:
- Lower heat input, resulting in reduced distortion and residual stresses
- Absence of filler material, eliminating the need for consumables
- Improved mechanical properties due to fine-grained microstructure in the weld zone
- Ability to join dissimilar materials and alloys that are challenging to weld using traditional methods
Understanding these fundamental principles is crucial for optimizing the FSW process and achieving high-quality welds consistently. The interplay between various process parameters significantly influences the material flow, heat generation, and ultimately, the weld quality.
Critical process parameters in FSW
Successful implementation of FSW relies on the careful control and optimization of several critical process parameters. These parameters not only affect the weld quality but also determine the efficiency and productivity of the welding operation. Let's explore the most influential parameters and their impact on the FSW process.
Tool rotation speed and its impact on weld quality
The tool rotation speed plays a crucial role in heat generation and material flow during FSW. Higher rotation speeds generally result in increased heat input and more extensive material stirring. However, excessively high speeds can lead to overheating and defect formation. Finding the optimal rotation speed is essential for achieving the desired balance between heat generation and material flow.
Optimal rotation speed ranges vary depending on the material being welded and the thickness of the workpieces. For example, aluminum alloys typically require rotation speeds between 800 and 1500 RPM, while steels may need lower speeds in the range of 200 to 500 RPM due to their higher melting points and lower thermal conductivity.
Traverse speed optimization for different materials
The traverse speed, also known as the welding speed, directly influences the heat input per unit length of the weld. Slower traverse speeds result in higher heat input and more thorough mixing of the material, while faster speeds can lead to insufficient heating and inadequate material flow. Optimizing the traverse speed is crucial for achieving the desired weld properties and productivity.
For aluminum alloys, typical traverse speeds range from 50 to 500 mm/min, depending on the alloy composition and thickness. Steels and other high-temperature alloys often require slower traverse speeds to ensure adequate heat generation and material flow. It's important to note that the relationship between rotation speed and traverse speed, often expressed as the weld pitch
, is a critical factor in determining weld quality.
Axial force control and weld penetration
The axial force applied to the FSW tool significantly affects weld penetration and the formation of defects. Insufficient axial force can result in lack of penetration and poor material consolidation, while excessive force may lead to overheating and tool wear. Proper control of the axial force is essential for achieving full penetration welds with minimal defects.
Tool tilt angle adjustment for enhanced material flow
The tool tilt angle, typically ranging from 0 to 3 degrees, influences material flow and weld surface quality. A slight tilt angle helps improve material consolidation at the trailing edge of the tool and reduces the formation of surface defects. However, excessive tilt can lead to uneven material distribution and reduced weld strength.
Advanced FSW tool designs and their effects
The design of the FSW tool plays a crucial role in determining the efficiency of the welding process and the quality of the resulting joint. Advanced tool designs can significantly improve material flow, heat generation, and weld properties. Let's explore some innovative tool designs and their effects on the FSW process.
Threaded pin tools vs. smooth pin tools
Threaded pin tools have become increasingly popular in FSW due to their enhanced material flow characteristics. The threads on the pin help to push material downward, improving vertical mixing and reducing the formation of voids or tunneling defects. In contrast, smooth pin tools rely primarily on friction and plastic deformation for material movement.
Scroll shoulder designs for improved surface finish
Scroll shoulder designs represent a significant advancement in FSW tool technology. These tools feature a spiral groove or scroll pattern on the shoulder surface, which helps to contain and direct the plasticized material inward towards the pin. The benefits of scroll shoulder designs include:
- Improved material flow and mixing
- Reduced flash formation and material loss
- Enhanced surface finish and appearance
- Increased process stability and repeatability
Scroll shoulder tools are particularly effective in applications where weld appearance is critical, such as in visible automotive or aerospace components. They also offer advantages in terms of reduced post-weld machining requirements and improved overall process efficiency.
Polygonal pin profiles and their influence on weld strength
Polygonal pin profiles, such as triangular, square, or hexagonal shapes, have gained attention for their ability to enhance material flow and increase weld strength. These non-circular profiles create a more complex stirring pattern compared to cylindrical pins, resulting in improved material mixing and a more refined grain structure in the weld zone.
Material-specific FSW parameter optimization
Different materials and alloy systems require specific FSW parameter combinations to achieve optimal weld quality. Understanding the unique characteristics and challenges associated with various materials is crucial for successful FSW implementation. Let's explore parameter optimization strategies for some common material groups.
Aluminum alloy series 2XXX, 5XXX, and 7XXX welding parameters
Aluminum alloys are among the most commonly welded materials using FSW, particularly in aerospace and automotive applications. Each alloy series presents unique challenges and opportunities for optimization:
Alloy Series | Typical Rotation Speed (RPM) | Typical Traverse Speed (mm/min) | Key Considerations |
---|---|---|---|
2XXX (Al-Cu) | 800-1200 | 100-300 | Susceptible to hot cracking, requires precise temperature control |
5XXX (Al-Mg) | 1000-1500 | 200-500 | Good weldability, may require higher speeds to avoid overheating |
7XXX (Al-Zn) | 600-1000 | 50-200 | Heat-sensitive, prone to softening in the heat-affected zone |
Optimizing FSW parameters for these alloy series often involves finding the right balance between heat input and material flow. For example, 7XXX series alloys typically require lower heat input to minimize softening in the heat-affected zone, while 5XXX series alloys can tolerate higher welding speeds due to their good weldability.
FSW parameters for dissimilar material joints
Joining dissimilar materials using FSW presents unique challenges due to differences in material properties, melting points, and flow characteristics. Successful parameter optimization for dissimilar joints often requires:
- Careful selection of tool positioning relative to the joint line
- Adjustment of rotation and traverse speeds to accommodate both materials
- Consideration of material-specific tool designs
- Fine-tuning of axial force and tilt angle to promote mixing
One common approach for dissimilar material FSW is to position the tool slightly offset towards the harder or higher-melting-point material. This technique helps ensure adequate heating and material flow in the more challenging material while preventing overheating of the softer material.
High-temperature alloy FSW: challenges and solutions
Friction stir welding of high-temperature alloys, such as steels, titanium alloys, and nickel-based superalloys, presents significant challenges due to their high strength and low thermal conductivity. Successful FSW of these materials often requires:
- Advanced tool materials with high wear resistance and thermal stability
- Specialized cooling systems to manage tool and workpiece temperatures
- Lower rotation speeds and traverse rates compared to aluminum alloys
- Higher axial forces to achieve adequate material plasticization
Recent advancements in tool materials, such as polycrystalline cubic boron nitride (PCBN) and tungsten-rhenium (W-Re) alloys, have expanded the possibilities for FSW of high-temperature materials. These developments, combined with optimized process parameters, are enabling the application of FSW to an increasingly diverse range of engineering materials.
Real-time process monitoring and control systems
Implementing robust monitoring and control systems is essential for ensuring consistent weld quality and process stability in FSW. Advanced sensing technologies and control algorithms enable real-time adjustment of process parameters, leading to improved weld quality and reduced defect rates.
Force control vs. position control in FSW
Two primary control modes are commonly used in FSW: force control and position control. Each approach has its advantages and limitations:
- Force Control: Maintains a constant axial force throughout the weld, adapting to variations in material thickness or properties
- Position Control: Maintains a constant tool plunge depth, offering simplicity and compatibility with standard CNC machines
Force control systems often provide superior weld quality and consistency, particularly when welding materials with variable thickness or properties. However, they require more sophisticated equipment and control algorithms compared to position control systems.
Acoustic emission monitoring for defect detection
Acoustic emission (AE) monitoring has emerged as a powerful tool for real-time defect detection in FSW. By analyzing the acoustic signals generated during the welding process, it's possible to identify and classify various types of weld defects, including:
- Lack of penetration
- Voids or tunneling defects
- Excessive flash formation
- Tool wear or damage
Integrating AE monitoring with adaptive control systems allows for rapid adjustments to process parameters, minimizing defect formation and improving overall weld quality. This technology is particularly valuable in high-value applications where weld integrity is critical, such as aerospace structures or pressure vessels.
Thermal imaging for temperature distribution analysis
Thermal imaging cameras provide valuable insights into the temperature distribution during FSW, enabling better control of heat input and material flow. By monitoring the temperature profile in real-time, operators can:
- Optimize tool rotation and traverse speeds
- Detect and prevent overheating or insufficient heating
- Ensure consistent temperature distribution across the weld
- Identify potential defect formation due to temperature anomalies
Advanced thermal imaging systems can be integrated with closed-loop control algorithms to automatically adjust process parameters based on the observed temperature distribution. This approach helps maintain optimal welding conditions and ensures consistent weld quality across a wide range of materials and thicknesses.
FSW parameter optimization techniques
Optimizing FSW parameters is a complex task due to the numerous variables involved and their interdependent relationships. Several advanced techniques have been developed to streamline the optimization process and achieve superior weld quality. Let's explore some of the most effective approaches.
Taguchi method for FSW parameter design
The Taguchi method is a powerful statistical approach for optimizing process parameters with minimal experimental runs. In FSW, this method can be applied to identify the most significant parameters and their optimal levels for achieving desired weld properties. Key steps in applying the Taguchi method to FSW include:
- Selecting appropriate control factors and their levels
- Designing the experimental matrix using orthogonal arrays
- Conducting experiments and measuring response variables
- Analyzing results using signal-to-noise (S/N) ratios
- Determining optimal parameter combinations
The Taguchi method is particularly useful for initial parameter screening and optimization, providing
The Taguchi method is particularly useful for initial parameter screening and optimization, providing valuable insights into the most influential factors affecting weld quality. However, it's important to note that this method assumes linear relationships between parameters and responses, which may not always hold true in complex FSW processes.
Response surface methodology in FSW optimization
Response Surface Methodology (RSM) is a powerful statistical technique for modeling and optimizing complex processes with multiple input variables. In FSW, RSM can be used to develop mathematical models that describe the relationships between process parameters and weld properties. The key advantages of RSM in FSW optimization include:
- Ability to capture non-linear relationships between parameters and responses
- Efficient exploration of the parameter space with a reduced number of experiments
- Generation of contour plots and response surfaces for visual analysis
- Simultaneous optimization of multiple response variables
Artificial neural networks for predictive modeling of FSW parameters
Artificial Neural Networks (ANNs) offer a powerful approach to modeling and predicting FSW process outcomes based on input parameters. Unlike traditional statistical methods, ANNs can capture complex, non-linear relationships between multiple input and output variables without requiring explicit mathematical formulations.
Key advantages of using ANNs for FSW parameter optimization include:
- Ability to handle large datasets with multiple input and output variables
- Capture of complex, non-linear relationships between parameters and weld properties
- Robust performance in the presence of noisy or incomplete data
- Potential for real-time prediction and optimization during welding
Recent advancements in machine learning techniques, such as deep learning and ensemble methods, have further enhanced the potential of ANNs in FSW parameter optimization. These advanced models can integrate data from multiple sources, including process parameters, material properties, and real-time sensor measurements, to provide more accurate and robust predictions of weld quality.
As the field of FSW continues to evolve, the integration of advanced optimization techniques like the Taguchi method, RSM, and ANNs will play a crucial role in expanding the applicability of this innovative welding process to new materials and challenging applications. By leveraging these powerful tools, engineers and researchers can accelerate the development of optimized FSW processes, leading to improved weld quality, increased productivity, and reduced development costs across various industries.