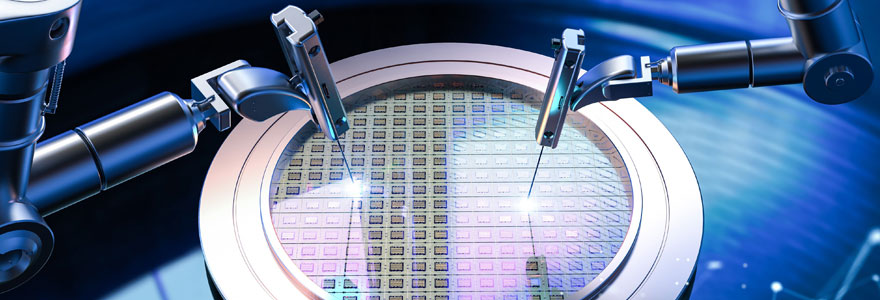
Semiconductor manufacturing is a process used to create chips, which are used in electronic devices and circuits. The manufacturing process begins with a silicon wafer, which is a thin slice of silicon. The wafer is then cleaned and coated with a layer of photoresist, which is a light-sensitive material. Next, the wafer is exposed to light, which creates a pattern on the photoresist. The wafer is then placed in a chemical bath, which removes the exposed photoresist. The remaining photoresist is used as a mask, and the wafer is etched with chemicals. Finally, the wafer is cleaned and polished.
How are semiconductor devices manufactured?
Semiconductor manufacturing is a complex process that involves numerous steps. The exact number of steps and the specific details of each step can vary depending on the type of semiconductor being manufactured. However, there are key steps that are essential to the semi-conductor production machine reconditioning department.
The first step is known as wafer preparation. In this step, a thin slice of semiconductor material, known as a wafer, is created. The wafer is then cleaned and polished to ensure that it is smooth and free of defects.
The second step is known as doping. In this step, impurities are introduced into the wafer to create the desired electrical properties.
The third step is known as lithography. In this step, a pattern is created on the wafer that will define the semiconductor device.
The fourth step is known as etching. In this step, the unwanted material is removed from the wafer, leaving behind the desired pattern.
The fifth step is known as deposition. In this step, materials are deposited onto the wafer to create the desired electrical properties.
The final step is known as packaging. In this step, the semiconductor device is encased in a package to protect it from the environment.
What is required for semiconductor manufacturing?
Semiconductor manufacturing is a process whereby electronic circuits are fabricated on semiconductor materials. Silicon is the most common material used in semiconductor manufacturing, though other materials such as germanium and gallium arsenide are sometimes used. The manufacturing process begins with the creation of a silicon wafer, which is a thin slice of silicon crystal. The wafer is then cleaned and coated with a layer of photoresist, which is a light-sensitive material.
Next, the wafer is exposed to a pattern of light which is used to transfer the circuit pattern onto the wafer. The exposed wafer is then developed, which removes the photoresist in the areas that were not exposed to light. The next step is etching, which uses chemicals to remove the exposed silicon in the areas that will become the circuit components.
The final step is to deposit metal onto the wafer to create the electrical connections between the components. The wafer is then cut into individual chips and packaged. Semiconductor manufacturing is a complex process with many steps, but the end result is the creation of electronic circuits that are the building blocks of modern electronic devices.
What is front end process in semiconductor?
In semiconductor manufacturing, the front-end process refers to everything that happens to the silicon wafer from the time it is cut from a crystalline ingot until it is ready for the back-end process. This includes cleaning, doping, lithography, etching and metallization. The front-end process is also sometimes referred to as the fabrication process.
The first step in the semiconductor manufacturing process is known as wafer slicing. In this step, a silicon ingot is cut into thin wafers using a diamond saw. The wafers are then cleaned using a process called chemical-mechanical polishing (CMP).
After the wafers are cleaned, they undergo a process called doping. In this process, atoms of other elements are added to the silicon crystal in order to create an electric field. The type of dopant atoms used will determine the type of semiconductor being created.
The next step is lithography. In this process, a light-sensitive material called photoresist is applied to the wafer. A mask is then placed over the wafer and exposed to light. This creates an image of the desired circuit pattern on the photoresist.
The exposed photoresist is then developed, which means the exposed areas are removed. The remaining photoresist protects the areas of the wafer that will not be etched.
The next step is etching. In this process, the unprotected areas of the wafer are selectively removed using chemicals or plasma. This leaves behind the desired circuit pattern.
The final step in the front-end process is metallization. In this process, metal is deposited on the wafer to create the electrical connections between the different components of the circuit.
The article discusses important steps in semiconductor manufacturing: cleaning, doping, lithography, etching, metallization, and testing. Each step is crucial to the manufacturing process and must be carefully controlled in order to produce high-quality semiconductor products.